Expanding the Improvement – Beyond PDSA
Expanding the improvement – beyond PDSA
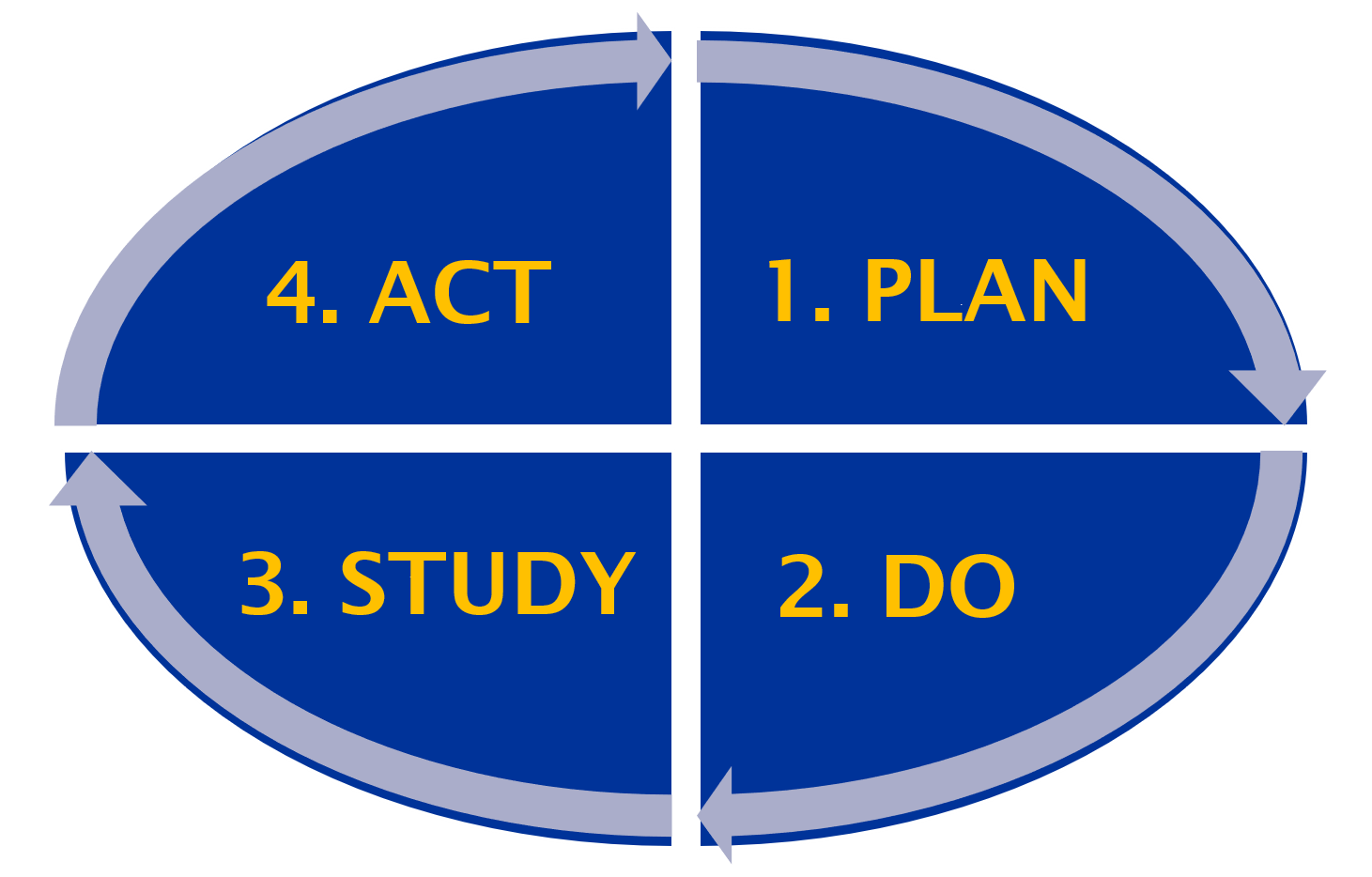
Let's use this year to build upon PDSA to create good change faster, easier, and with better results.
We begin the year with a focus on the basic steps for making change and improvements: the PDSA improvement cycle.
The improvement cycle, originally known as the Shewhart Cycle (1940), was used for conducting an experiment . In 1950 Deming expanded it to illustrate its ongoing nature and terminology of Plan-Do-Check-Act. 35 years later Deming changed it to Plan-Do-Study-Act, to emphasize the importance of learning.
The PDSA improvement cycle has continued to evolve (1985-today) into generalized data/information-based problem solving by Deming, Toyota (“A3” problem solving), Six Sigma, and others.
PLAN: ◊ Frame the problem-gap & goal ◊ Understand the current process ◊ Collect and evaluate date ◊ Identify root causes and solutions ◊ Develop the Improvement hypothesis
DO: ◊ Develop the solutions ◊ Test potential solutions ◊ Measure results
STUDY: ◊ Analyze results and determine impact (Will the goal be reached?) ◊ Extract lessons learned to identify additional actions or tests
ACT: ◊ Effectively install the new solutions ◊ Measure outcomes ◊ Coach & continue improving
Abraham Maslow says, "If the only tool you have is hammer, you tend to see every problem as a nail". PDSA is the backbone for many improvement tools and methods (tools that follow the improvement cycle) so let's build upon PDSA and expand your improvement toolkit. Advanced improvement methods use PDSA however are often tailored to specific types of problems or to eliminate specific forms of waste (regardless of your processes, industry, or team dynamics).
Here are some advanced improvements methods to learn-apply-advance your improvement impact:
5S + VISUAL CONTROLS – Decrease time searching for information, material, people, or equipment. Sort, Shine, Straighten, Standardize, Sustain, (+ Safety). Benefits included 35% productivity and 20% climate engagement.
KAIZEN– Don’t wait for results. Get improvements rapidly (5 days) with the team-based systematic problem-solving process that flows through all phases of the improvement cycle. It is one of the most versatile and impactful methods. Benefits included 70% decrease in labor hours (575 to 175 hours per item) along with less frustration and overtime; shorter cycle time; and more standardized, consistent, and quality product.
MISTAKE PROOFING - A systematic approach to reduce defects associated with “human error” and avoid the rework costs resulting from those defects. Benefits included 99.8% improvement in data entry accuracy.
SIX SIGMA - A disciplined, data-driven approach to reduce defects and variation in processes and products. With the high level of data analysis, the 4-steps are broken down into 5 steps: Define, Measure, Analyze, Improve, and Control. Benefits included reduced process variation.
STRATEGIC & ANNUAL PLANS - Yes, this also uses the PDSA cycle. Align long-term and short-term priorities, resources, and actions to achieve your organization’s goals using a data-based strategic and annual planning process. Benefits included more focus, alignment, more strategies accomplished, and bigger performance measure impact.
FLOW – Decrease WAIT time within and between steps by balancing work content, sequencing tasks to one unit at a time, and introducing visual controls between work steps. Benefits included 75% decrease in cycle time, 50% increase in process capacity, 95% on-time reliability, and 40% decrease in inventory.
INNOVATION PROCESS – A process to create innovative, transformative processes, products, or services with immediate and long-term impact and benefits. Within the process several additional analytical techniques are utilized, including quality function development, value stream mapping, failure mode effect analysis, and TRIZ. Benefits included increased customer loyalty and market growth.
QUICK CHANGE / SMED - Reducing the waste of getting ready to do work or perform value added tasks by assessing each task of a changeover process to distinguish what can be done externally to the process and what cannot. Work is then redesigned to eliminate tasks, move external ones out of the changeover process and streamline all remaining activities. Benefits included 94% decrease in changeover times (90 to 5 minutes).
VALUE ENGINEERING / DESIGN FOR EXCELLENCE - Improve and simplify designs or processes to provide the lowest cost solution to meet the functional needs of the customer and where every component and activity is challenged to bring value. Benefits included simplified process design, reduced costs, and increased customer satisfaction.
The performance of your organization relies on development and use of both basic and advanced skills. Your personal challenge is to keep on developing skills and bringing more value by creating even more impactful improvements,